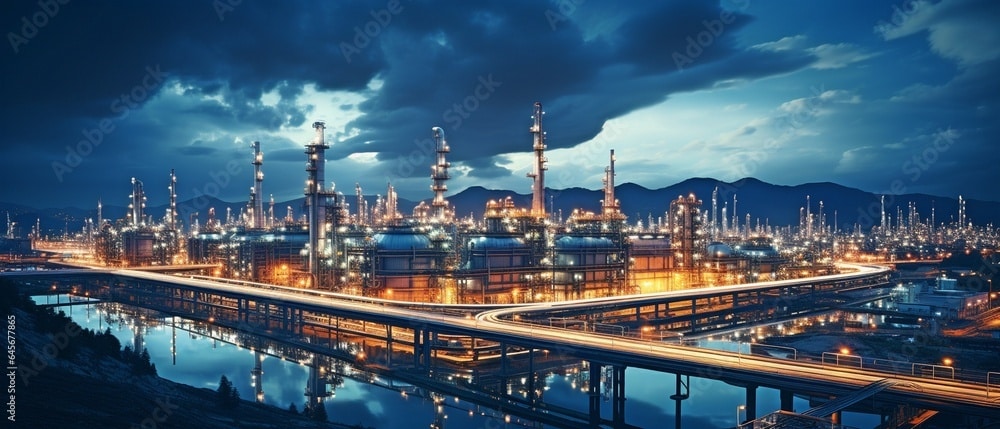
Becht Explores High-Temp Corrosion in Renewable Diesel & Aviation Fuel Production
In recent years, the production of renewable diesel and sustainable aviation fuels from biological sources, particularly natural oils, has experienced remarkable growth. This surge is largely driven by global climate change initiatives mandated by governments worldwide, coupled with the increasing emphasis on carbon capture and sequestration. As a result, substantial investments have been made in retrofitting and adapting existing refinery hydroprocessing infrastructure to accommodate natural oils or blends of natural oils with crude oil, facilitating the production of RD and SAF.
The rationale behind these investments lies in the molecular compatibility of natural oils with mid-distillate fuel products like diesel and aviation fuel, as well as the optimization of hydroprocessing units for the removal of unwanted sulfur and oxygen compounds. In modified hydroprocessing applications, the high-temperature decomposition of triglycerides leads to the production of RD and SAF through the hydroprocessing of esters and free fatty acids. The resulting oxygen-free RD and SAF products are fully interchangeable with petroleum hydrocarbons.
However, hydroprocessing of refined natural oils presents its own set of challenges, particularly in terms of corrosion. To address this issue, the authors have developed a molecular mechanistic model to quantify simultaneous high-temperature corrosion caused by naphthenic acids and sulfidation in refinery operations. This model, known as CorrExpert®-Crude, has been adapted to address high-temperature FFA corrosion, given the similarities between FFA and naphthenic acids.
A crucial aspect of modelling corrosion for FFA is understanding the inhibitive role of hydrogen in the presence of iron sulphide species. Although natural oils do not contain sulphur compounds, reactive sulphur species present in coprocessing applications facilitate the formation of a potentially protective nano barrier layer of iron sulphide. Additionally, FeS acts as a catalyst for the reduction of FFA through atomic hydrogen, generated from the dissociation of molecular hydrogen.
The prediction model incorporates factors such as hydrogen partial pressure, residence time, and reactive sulfur concentration to assess FFA corrosion risk for various commonly used natural oils in renewable applications. By considering these parameters, the model provides a comprehensive framework for evaluating corrosion risk and metallurgical performance in RD/SAF units. This pioneering solution offers an easy-to-use tool to enhance the reliability of unit piping and equipment in renewable fuel production facilities.
By: Storage Terminals Magazine, April 15, 2024