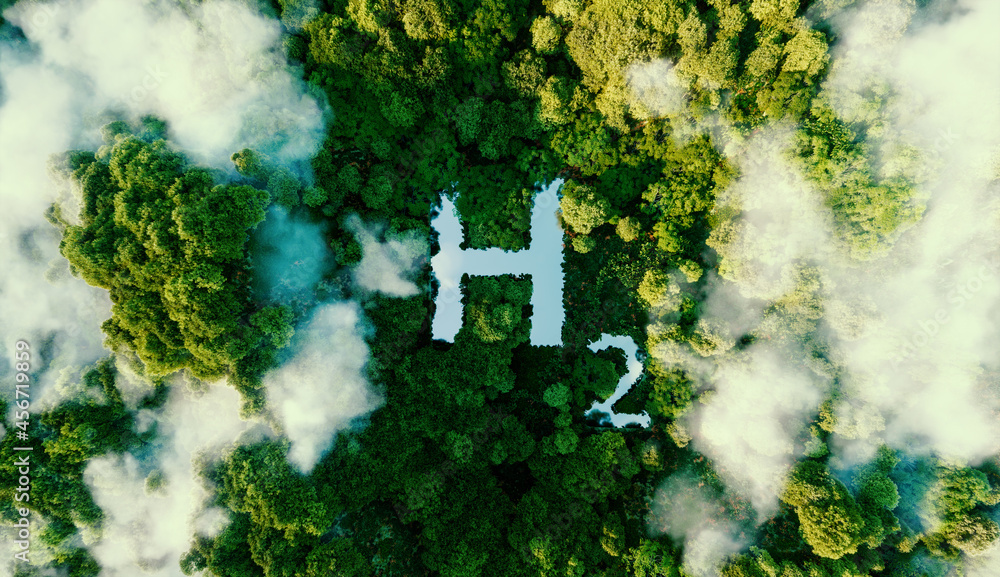
The Future of Hydrogen Testing for Fueling & Storage Applications
Hydrogen is traditionally used to produce methanol and refine petroleum. Currently, around 51% of hydrogen used in the economy goes to refineries, and 43% is used as an input for ammonia synthesis, primarily for production of fertilizers.1 The most common process for producing hydrogen is steam methane reforming. Fossil fuel-based, it consumes around 6% of the world’s natural gas and 2% of its coal.
However, this is changing as the production of green hydrogen (see sidebar) becomes a more viable option, and to some extent, an essential one as fossil fuels become more expensive, more unacceptable due to climate change and a bargaining tool in geopolitical conflicts. The world is looking to more sustainable energy production and ways to reach net zero emissions by the year 2050,2 and using hydrogen as fuel for heavy transport applications like trucks, buses and cars is an increasingly popular topic of conversation. However, using green hydrogen comes with its own challenges, including how to store and transport it and how to test and validate it where no standard testing and
Green hydrogen is used to describe hydrogen gas that is completely carbon-neutral and produced using renewable energy sources in a process called electrolysis. Here are its key characteristics:
1. Renewable energy source: Green hydrogen is produced using electricity generated only from renewable energy sources, such as wind, solar, hydroelectric or geothermal power.
2. Electrolysis: Green hydrogen is produced in an electrolyzer, which uses renewable energy to split water (H2O) into hydrogen (H2) and oxygen (O2) using an electric current.
3. Zero greenhouse gas emissions: Because the electricity used in the electrolysis process comes from renewable sources, the overall carbon footprint of green hydrogen production is minimal or even zero.
4. Versatile applications: Green hydrogen can be used in a wide range of applications, including fuel cell vehicles, industrial processes, electricity generation and energy storage. It can serve as an energy carrier, helping to store and transport renewable energy efficiently.
Sealing & Storage
Achieving a reliable seal involves using advanced materials and engineering techniques that can withstand the challenges posed by hydrogen’s small molecular size, which makes it difficult to seal and store as it can permeate through many materials. For certain applications, sealing materials must demonstrate a high level of compatibility and permeation resistance to prevent loss.
Another related issue is rapid gas decompression (RGD). In a high-pressure system, the small hydrogen molecules can be absorbed into a seal material. If the pressure in the system is suddenly relieved, gas trapped in the seal material can expand to match the new ambient pressure, potentially causing the seal to blister and crack as the gas tries to escape.
Finally, seals for different hydrogen systems need to withstand seriously tough environments, including high pressures of up to 14,504 pounds per square inch (psi) (e.g., in high-pressure valves) and extreme low temperatures down to -418 F (e.g., in liquid hydrogen storage and transportation).
Hydrogen: The Facts (Sidebar)
Hydrogen is a gas with an average atomic mass of 1.00794.
It is the first and most abundant element on the periodic table.
It is a constituent of most organic compounds, making up about 75% of the universe’s overall mass.
Hydrogen is colorless, odorless and tasteless.
The lightest of all elements, hydrogen consists of the smallest of all molecules, which means it can permeate through many materials.
Hydrogen is rarely available in its pure form on Earth, so it requires extraction from compounds containing hydrogen. Any compound with ‘H’ in its chemical formula has hydrogen as one of its constituents.
It is in hydrocarbons, methane (CH4) and water (H2O).
Setting the Standard
The evolving nature of the hydrogen market and value chain creates a demand for fuel storage standards. Experts are looking to existing standards for similar storage applications such as those used for oil and gas, which define acceptable characteristics for polymers in arduous conditions relative to permeation, RGD and general media compatibility. However, no existing standards provide a perfect fit, because they do not account for the conditions seen in typical applications throughout the hydrogen value chain.
Hydrogen is an explosive gas, and it must be tested with great care. Many seal manufacturers use third-party testing facilities. Helium is often used as a proxy for safer testing, and results are converted to hydrogen values. However, helium is not a perfect substitute, and some companies are investing in their own rigs that are approved to test hydrogen. These facilities offer comprehensive, hydrogen-specific standards and validation processes, and their experts can create custom solutions for whatever the user needs.
Seals are tested to International Organization for Standardization (ISO) 17268 for RGD, EC79 for components intended for hydrogen-powered vehicles, SAE J2600 for fueling connectors, nozzles and receptacles of compressed hydrogen surface vehicles, along with some permeation testing. Other tests include verification for a wide range of static sealing cross sections, including cyclic pressure, with pressure ranges from 101 to 10,877 psi and temperature ranges
from -65 F to 266 F.
The current and future market needs for hydrogen sealing across the entire value chain production, transportation, storage and end use are broad, ranging from standard components to highly engineered solutions. Few OEMs have extensive experience in these areas, making a hydrogen component and sealing partner essential.
By: pumpsandsystems / James Simpson, 03/12/2024.